Overfill Prevention Equipment Inspection Info
Overfill prevention is essential to the integrity and safety of your underground storage tanks. Have your overfill prevention equipment inspected within deadlines to be in compliance with the New requirements of the California Code of Regulations. Learn more about these important regulations here.
Inspection Requirements and Process Details:
As of October 1, 2018, all overfill prevention equipment used to comply with California Code of Regulations must be inspected periodically and after repairs. Inspections may occur at least once every 36 calendar months after the first inspection is completed. In addition to the periodic inspections, an inspection is required within 30 days of the date of the completion of a repair to the overfill prevention equipment to ensure that it is in proper functioning order.
Repairs are required any time the overfill prevention equipment ceases to operate properly and causes the UST to be out of compliance with UST requirements.
Before performing the inspection, the UST owners or operators must notify their UPA at least 48 hours before conducting the inspection. The notification provides an opportunity to the UPA to incorporate the inspection into their schedule so that they can witness the inspection. However, the UPA is not required to be present for the inspection to occur.
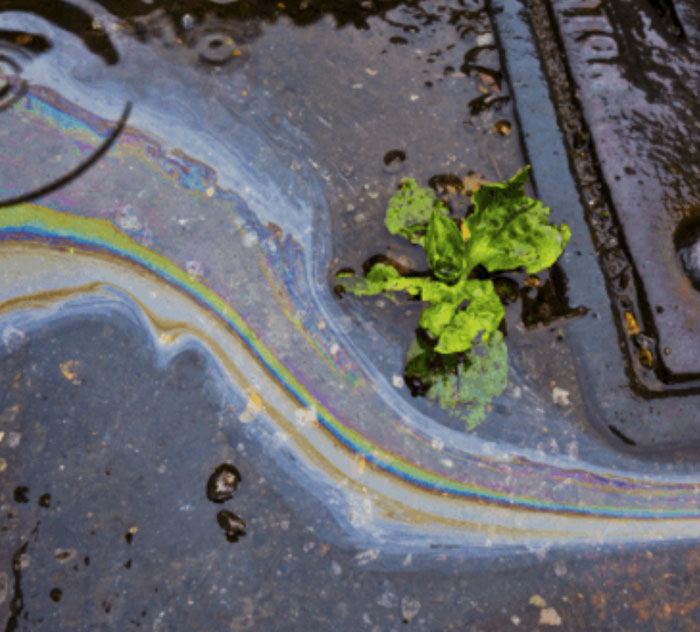
Reach Out To Us:
(909) 838-3231
Inspection Details
Manufacturer guidelines must be used if the guidelines meet the inspection criteria as defined below. If manufacturer guidelines do not exist or the manufacturer guidelines do not meet the inspection criteria, you must use an industry code or engineering standard, such as Petroleum Equipment Institute’s Recommended Practices 1200. If there are no manufacturer guidelines, industry codes, or engineering standards, or they do not meet the inspection criteria, then you must use a method developed by a California registered professional engineer.
The inspection procedure used will determine inspection activities such as removing the drop tube from the tank or flow restrictors from the vent piping.
At a minimum, the inspection criteria for overfill prevention equipment must determine: 1) if the equipment is set at the correct level in the tank; and 2) if the equipment will activate when the substance stored reaches that level. A assing result is when the overfill prevention equipment inspected is set at the correct level, and the equipment is in a condition that it will activate when the stored substance reaches that level. If the overfill prevention equipment fails the inspection, the UST service technician must explain why the equipment failed.
Inspection Documentation
The results of the inspection must be recorded on the Overfill Prevention Equipment Inspection Report Form. A copy of the procedure used to inspect the equipment must be attached to the form, along with any data collected to determine if the overfill prevention equipment “passed” or “failed” the inspection. The completed Overfill Prevention Equipment Inspection Report Form,” the attached procedure, and data collection must be submitted to the Unified Program Agency (UPA) within 30 days from the date of the inspection by hand-delivery, mail, facsimile, or other electronic methods.
The UST owner or operator must retain a copy of the inspection report on-site, or offsite at a readily available accessible location if approved by the local agency.
For more details, refer to the Overfill Prevention Equipment Inspection Requirements California Code of Regulations: (link: Overfill Prevention Equipment Inspection Requirements California Code of Regulations, Title 23, Division 3, Chapter 16, Section 2637.2).